Automation Tray
Introduction
One of our customers has been investing in automation equipment to automate their production line. This automation will increase their output with 20%, using less operators.
These lines use thermoformed trays in which the components are packed, and they then need to be picked up by a pick & place robot. However, there was an issue with the accuracy of the system, the robot sometimes missed the component, which caused the line to go into alarm, thus stopping the production.
After investigating the problem, they found that the robot was ok, but that the tray wasn’t always in the exact same location. Since the robot uses small suction cups which need to be positioned on predetermined locations in order to function, misalignment caused the line to stop time after time.
Get in touch
No matter what your manufacturing project, Alacami is here to help. We have an in-house team of design engineers and incorporated post-production services to help us run your project smoothly from start to finish. Contact us today to learn more about what we can do for you.
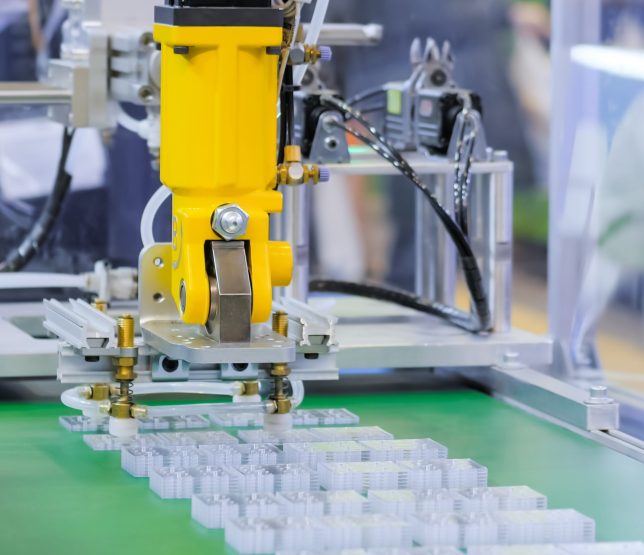
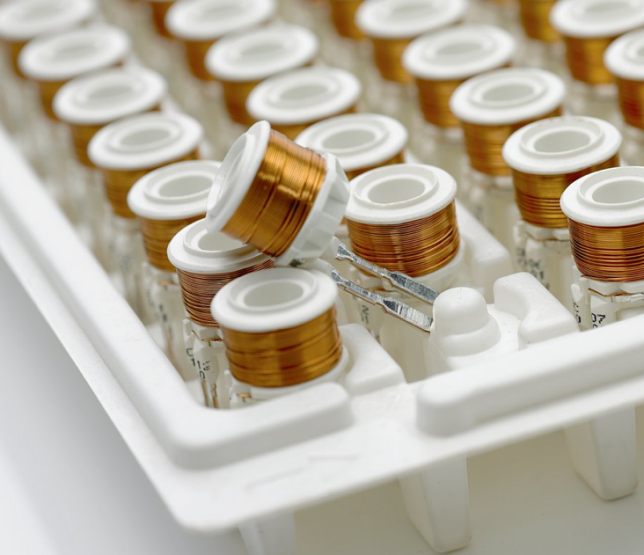
We were contacted by the customer asking us what we could do to improve the issue. As such we started an investigation with our customer to see what could be done to solve this problem.
During the investigation we found out that the tray was being aligned on the cutting edge. Now in thermoforming, we have 2 processes, the forming process and the cutting process. These happen in the same machine, but in a different station. Meaning there is always a tolerance on the cutting edge in relation to the cavity where the product sits. This is a cause the robot to go in alarm.
We were contacted by the customer asking us what we could do to improve the issue. As such we started an investigation with our customer to see what could be done to solve this problem.
During the investigation we found out that the tray was being aligned on the cutting edge. Now in thermoforming, we have 2 processes, the forming process and the cutting process. These happen in the same machine, but in a different station. Meaning there is always a tolerance on the cutting edge in relation to the cavity where the product sits. This is a cause the robot to go in alarm.
Next to that, the edge of the tray was a bit flexible. Meaning if the tray came into the loading station of the robot, sometimes it would flex and the position would be compromised again.
So we had 2 issues to solve, and both were inherently linked to our process, meaning getting this to almost zero tolerance would require quite a lot of changes. Thicker material to make the edge stronger, potential offline cutting with precision centering in order to avoid the tolerance difference between the tray edge and product cavity.
After meeting up with the team and a few discussions we did find a better solution which didn’t require any additional costs.
We decided to work on the body of the tray as a reference for the positioning of the tray instead of using the cutting edge of the tray. The reason being that the body of the tray in relation to the positioning of the component, never changes. The forming is done in 1 station, so the center of the cavity versus the formed side of the tray is fixed within 0,1mm. Misalignment is not an issue anymore.
After working with the customer on which areas to use as a location point, they modified these centering points and the system has been running smoothly ever since.
The background here is that as tray designers it’s important to firmly know the application so we can anticipate issues before they arise.
The Alcami team has 20+ years of experience in this kind of applications, and will gladly work with you to support your requirements.
Get in Touch - We Can Help
Alcami combines different production technologies allowing us to provide a turnkey solution for a variety of parts. We combine this with sourcing and logistics services, so our customers don’t need to worry about shipping and storage.