News
Plastic Thermoforming: A Comprehensive Guide
Plastic Thermoforming, is one of the primary services we at Alcami Global specialize in. This blog post provides a high-level introduction to this technology. To learn more about the Plastic Thermoforming solutions we offer, including cleanroom a manufacturing, click here.
Key Takeaways
- Plastic thermoforming is a manufacturing process that involves heating a plastic sheet and forming it into a desired shape using a mold.
- Thermoforming offers advantages in product design such as cost-effectiveness, versatility, and the ability to create complex shapes.
- Different types of plastic materials can be used in thermoforming, including ABS, PVC, and polycarbonate.
Get in touch...
No matter what your manufacturing project, Alcami is here to help. We have an in-house team of design engineers and incorporated post-production services to help us run your project smoothly from start to finish. Contact us today to learn more about what we can do for you.
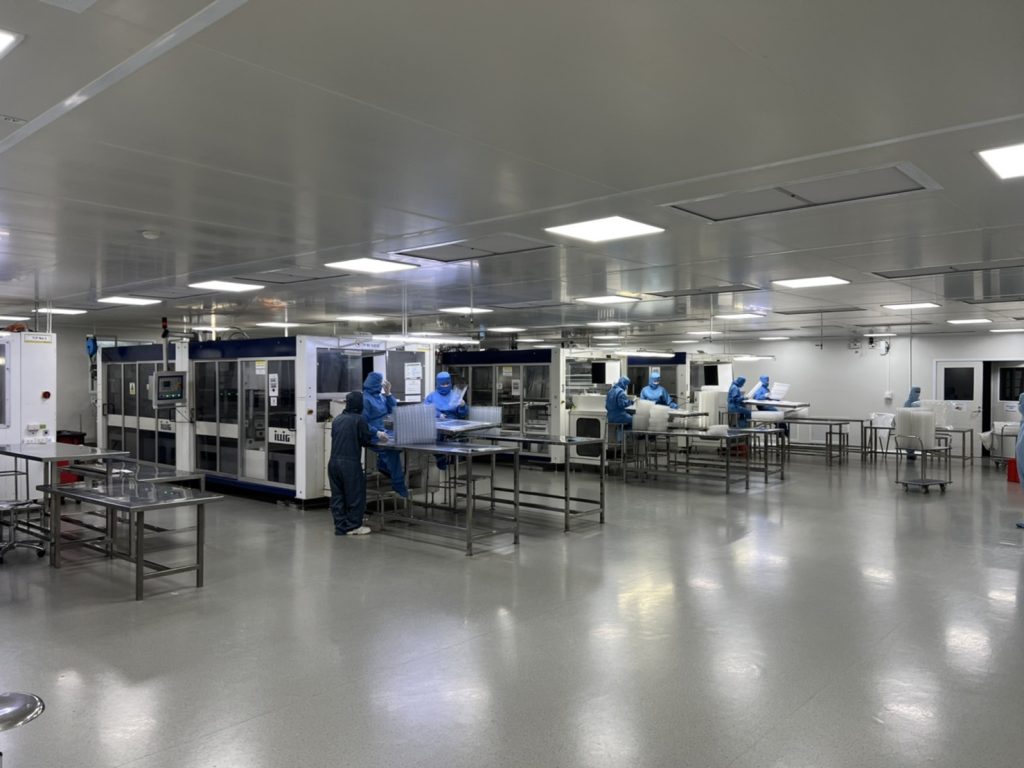
Plastic Thermoforming - Introduction
Plastic Thermoforming is a process that involves heating a plastic sheet and forming it into a specific shape using a mold. This process is widely used in product design and part manufacture due to the advantages it offers:
- Cost-effectiveness
- Design versatility
- Fast turnaround time
- Scalability for large quantities.
Plastic thermoforming has become an integral part of the product design process, allowing designers to create innovative and functional products.
The History of Plastic Thermoforming
The origins of thermoforming can be traced back to ancient civilizations where materials such as clay and wood were heated and molded into various shapes. However, the modern thermoforming process as we know it today began to emerge in the early 20th century.
The evolution of thermoforming technology can be attributed to advancements in materials and machinery. In the 1930s, the development of new plastic materials such as polystyrene and polyvinyl chloride (PVC) paved the way for the growth of thermoforming. These materials were lightweight, durable, and easy to mold, making them ideal for thermoforming applications.
Major milestones in thermoforming history include the invention of the first vacuum forming machine in the 1940s and the introduction of computer-aided design (CAD) and computer-aided manufacturing (CAM) technologies in the 1980s. These advancements revolutionized the thermoforming industry, allowing for more precise and efficient production processes.
Plastic Thermoforming Product Design Benefits
Cost-effectiveness
One of the main advantages of plastic thermoforming in product design is its cost-effectiveness. Compared to other manufacturing processes such as injection molding or blow molding, thermoforming requires less initial investment in tooling and equipment. This makes it an ideal choice for small to medium-sized production runs or for products with complex shapes that are not suitable for other processes.
Design versatility
Another advantage of plastic thermoforming is its versatility in design. Thermoforming allows designers to create products with intricate details, textures, and complex shapes that would be difficult or expensive to achieve with other processes. The flexibility of the plastic sheet allows for the creation of unique designs that can be customized to meet specific requirements.
Quick turnaround time
Additionally, plastic thermoforming offers a quick turnaround time. The process is relatively fast compared to other manufacturing processes, allowing for shorter lead times and faster production cycles. This is especially beneficial for companies that need to bring products to market quickly or respond to changing market demands.
Scalability for large quantities
Lastly, plastic thermoforming has the ability to produce large quantities of products efficiently. The process can be easily scaled up to meet high-volume production needs, making it suitable for industries that require mass production of products.
Cost-Effective Product Design with Thermoforming
Thermoforming offers several cost-saving benefits compared to other manufacturing processes. One of the main cost-saving benefits of thermoforming is its low tooling costs. Unlike injection molding or blow molding, thermoforming does not require expensive molds or dies. This makes it a cost-effective option for small to medium-sized production runs or for products with complex shapes.
Thermoforming also offers material savings as it allows for efficient use of plastic materials. The process uses only the amount of material needed to form the product, minimizing waste and reducing material costs.
Additionally, thermoforming has lower labor costs compared to other manufacturing processes. The process can be automated to a certain extent, reducing the need for manual labor and increasing production efficiency.
When compared to other manufacturing processes such as injection molding or blow molding, thermoforming offers shorter lead times and faster production cycles. This allows companies to bring products to market quickly and respond to changing market demands more effectively.
Common Thermoforming Industrial Applications
Thermoforming is widely used in various industries due to its versatility and cost-effectiveness. Some industries that commonly use thermoforming include packaging, automotive, aerospace, medical, and consumer goods.
Packaging
In the packaging industry, thermoforming is used to produce trays, clamshells, blister packs, and other packaging materials. Thermoformed packaging offers excellent product protection, visibility, and customization options.
Automotive
In the automotive industry, thermoforming is used to produce interior and exterior parts such as dashboards, door panels, and bumpers. Thermoformed automotive parts offer lightweight, durable, and cost-effective solutions.
Aerospace
In the aerospace industry, thermoforming is used to produce interior components such as seat backs, tray tables, and overhead bins. Thermoformed aerospace components offer weight savings and design flexibility.
Medical
In the medical industry, thermoforming is used to produce medical trays, surgical instrument trays, and other medical devices. Thermoformed medical products offer sterile packaging solutions and customization options.
Consumer goods
In the consumer goods industry, thermoforming is used to produce a wide range of products such as toys, electronics enclosures, and household items. Thermoformed consumer goods offer design flexibility, durability, and cost-effectiveness.
The Thermoforming Process: Step-by-Step Guide
The thermoforming process involves several steps, each of which is crucial in achieving successful thermoforming. The process can be divided into three main stages: preheating, forming, and finishing.
1. Preheating
The first step in the thermoforming process is preheating the plastic sheet. The sheet is heated to a specific temperature until it becomes pliable and can be easily formed. This is typically done using a heating oven or infrared heaters.
2. Forming
Once the plastic sheet is heated, it is transferred to the forming station where it is placed over a mold. The mold is then closed, and vacuum or pressure is applied to shape the plastic sheet around the mold. This creates the desired shape of the product.
3. Cooling and finishing
After the forming process, the product is cooled to solidify the plastic and maintain its shape. This can be done using cooling fans or water sprays. Once cooled, the product is trimmed and finished to remove any excess material or imperfections.
Design Considerations for Successful Thermoforming
Successful thermoforming requires careful consideration of various design factors. Some key design considerations for thermoforming include:
- Material selection
- Mold design
- Draft angles
- Undercuts
- Wall thickness.
Material selection
Material selection is an important factor in thermoforming as different materials have different properties and characteristics. It is important to choose a material that is suitable for the intended application and can withstand the required environmental conditions.
Mold design
Mold design plays a crucial role in achieving successful thermoforming. The mold should be designed to allow for easy removal of the formed part without causing any damage or distortion. It should also be designed to ensure uniform heating and cooling of the plastic sheet.
Draft angles
Draft angles are necessary in thermoforming to allow for easy removal of the formed part from the mold. A draft angle is a slight taper added to the vertical walls of the mold, which allows the part to be released smoothly without getting stuck.
Undercuts
Undercuts are features in the design that prevent the part from being easily removed from the mold. It is important to minimize or eliminate undercuts in thermoforming to ensure easy release of the formed part.
Wall thickness
Wall thickness is another important design consideration in thermoforming. The thickness of the plastic sheet should be uniform throughout the part to ensure even heating and cooling. Uneven wall thickness can result in warping or distortion of the formed part.
Plastic Materials Used in Thermoforming
Type of Plastic | Properties | Applications |
Polyethylene (PE) | Flexible, durable, chemical resistant | Food packaging, toys, household items |
Polypropylene (PP) | Stiff, heat resistant, chemical resistant | Food packaging, automotive parts, medical devices |
Polystyrene (PS) | Rigid, lightweight, good insulation | Food packaging, disposable cups, CD cases |
Polyvinyl Chloride (PVC) | Tough, weather resistant, flame retardant | Construction materials, electrical cables, medical tubing |
Polyethylene Terephthalate (PET) | Clear, strong, lightweight | Beverage bottles, food packaging, textiles |
There are various types of plastic materials used in thermoforming, each with its own unique properties and characteristics. Some common types of plastic materials used in thermoforming include polystyrene (PS), polyethylene terephthalate (PET), polypropylene (PP), and acrylonitrile butadiene styrene (ABS).
Polystyrene
Polystyrene is a versatile plastic material that is commonly used in thermoforming applications. It is lightweight, rigid, and has good impact resistance. Polystyrene is often used for packaging materials, disposable cups and containers, and automotive parts.
Polyethylene Terephthalate
Polyethylene terephthalate is a transparent plastic material that is commonly used for packaging applications such as bottles and trays. It has excellent clarity, good chemical resistance, and is easily recyclable.
Polypropylene
Polypropylene is a durable and flexible plastic material that is commonly used for packaging, automotive parts, and consumer products. It has good chemical resistance, high impact strength, and can withstand high temperatures.
Acrylonitrile butadiene styrene
Acrylonitrile butadiene styrene is a tough and rigid plastic material that is commonly used for automotive parts, electronic enclosures, and consumer products. It has good impact resistance, high heat resistance, and is easily molded into complex shapes.
Sustainability and Environmental Benefits of Thermoforming
Thermoforming offers several sustainability and environmental benefits compared to other manufacturing processes. One of the main environmental benefits of thermoforming is its ability to use recycled materials. Thermoformed products can be made from recycled plastic materials, reducing the demand for virgin plastics and minimizing waste.
Thermoforming also produces less waste compared to other manufacturing processes. The process uses only the amount of material needed to form the product, minimizing scrap and reducing landfill waste.
Additionally, thermoforming has a lower carbon footprint compared to other manufacturing processes. The process requires less energy and resources, resulting in lower greenhouse gas emissions and reduced environmental impact.
Future of Thermoforming: Innovations and Advancements
The future of thermoforming looks promising with ongoing innovations and advancements in technology. One of the current innovations in thermoforming technology is the use of 3D printing for mold production. 3D printed molds offer faster turnaround times and lower costs compared to traditional mold-making methods.
Another advancement in thermoforming technology is the use of robotics and automation. Robotic systems can be used to automate various steps in the thermoforming process, increasing production efficiency and reducing labor costs.
Furthermore, advancements in material science are leading to the development of new plastic materials that offer improved properties and characteristics for thermoforming applications. These materials may offer enhanced strength, heat resistance, or recyclability, opening up new possibilities for product design.
Conclusion
In conclusion, plastic thermoforming is a versatile and cost-effective manufacturing process that plays a crucial role in product design. It offers numerous advantages such as cost-effectiveness, versatility in design, quick turnaround time, and the ability to produce large quantities. Thermoforming has a rich history that has evolved over time with advancements in materials and technology. The process involves several steps that require careful consideration of design factors to achieve successful thermoforming. Thermoforming has applications in various industries and offers sustainability and environmental benefits compared to other manufacturing processes. With ongoing innovations and advancements, the future of thermoforming looks promising with new possibilities for product design.
Plastic Thermoforming FAQs
What is plastic thermoforming?
Plastic thermoforming is a manufacturing process that involves heating a plastic sheet to a pliable temperature, then forming it into a specific shape using a mold.
What types of plastics can be used in thermoforming?
A wide range of plastics can be used in thermoforming, including polystyrene, polyethylene, polypropylene, PVC, and PET.
What are the advantages of plastic thermoforming?
Plastic thermoforming offers several advantages, including low tooling costs, fast production times, and the ability to create complex shapes and designs.
What are the different types of thermoforming?
There are three main types of thermoforming: vacuum forming, pressure forming, and twin-sheet thermoforming.
What is the difference between thermoforming and injection molding?
Thermoforming involves heating a plastic sheet and forming it into a shape, while injection molding involves injecting molten plastic into a mold. Thermoforming is typically used for low to medium volume production, while injection molding is used for high volume production.
What is the environmental impact of plastic thermoforming?
Plastic thermoforming can have a lower environmental impact than other manufacturing processes, as it produces less waste and uses less energy. However, the use of plastic in general can have negative environmental consequences if not properly disposed of or recycled.
Get in Touch - We Can Help
Alcami combines different production technologies allowing us to provide a turnkey solution for a variety of parts. We combine this with sourcing and logistics services, so our customers don’t need to worry about shipping and storage.