News
Working with Antimicrobial & Disinfectant-Compatible plastics
With an ever-growing market interest in healthier and more hygiene-focused products, the demand for antimicrobial and disinfectant-compatible plastics is surging. In 2023, the market size was valued at USD 43.94 billion and is projected to reach USD 85.43 billion by 2032, growing at a compound annual growth rate (CAGR) of 7.7%. This expansion reflects the rising need for materials that offer both antimicrobial properties and long-term durability, particularly in sectors such as healthcare, packaging, and consumer goods, particularly within the consumer electronics and medical device industries.
Antimicrobial and disinfectant-compatible plastics reduce the risk of microbial contamination and boost products’ longevity and safety. This article provides a comprehensive introduction to the properties, benefits and best usage practices for these materials.
What are Antimicrobial Plastics?
Antimicrobial plastics are engineered to inhibit the growth of microorganisms such as bacteria, mold, and fungi on their surfaces. These materials incorporate antimicrobial agents, which can be embedded into the plastic during the manufacturing process or applied as a surface treatment. In consumer electronics, antimicrobial plastics are used to enhance the hygiene of frequently handled devices like smartphones, tablets, and remote controls. Similarly, in the medical device industry, these materials are critical in reducing infection risks associated with medical equipment and surfaces in healthcare settings.
Get in touch...
No matter what your manufacturing project, Alcami is here to help. We have an in-house team of design engineers and incorporated post-production services to help us run your project smoothly from start to finish. Contact us today to learn more about what we can do for you.
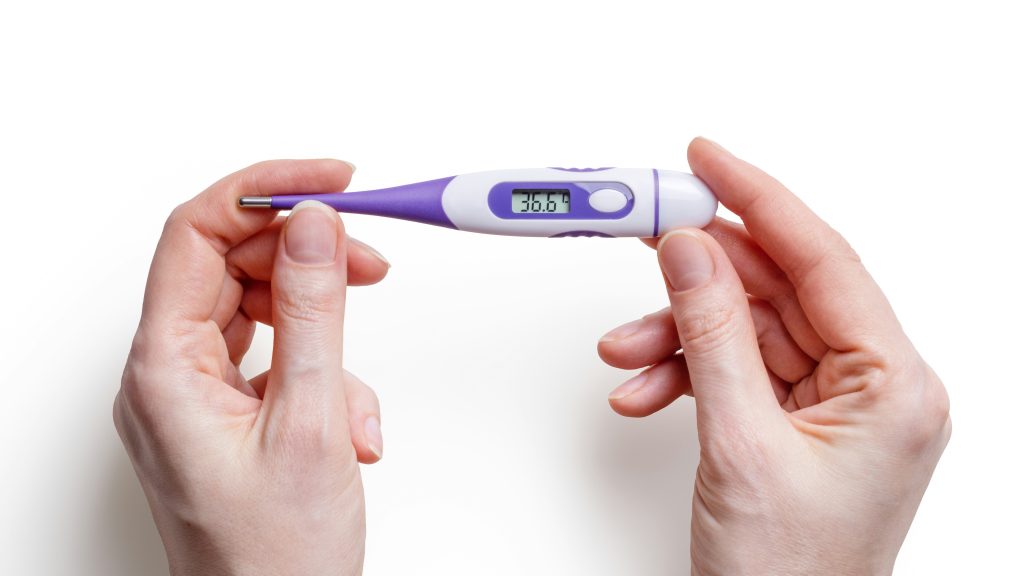
A Brief History of Antimicrobial and Disinfectant-Compatible Plastics
The increasing need for improved hygiene and infection control in various industries led to a growing interest in development of antimicrobial and disinfectant-compatible plastics, starting around the mid-20th century. Early research focused on incorporating known antimicrobial agents such as silver ions and copper into plastic materials.
The advent of more sophisticated polymer technologies in the 1970s enabled more effective and durable antimicrobial treatments. A notable example from the 1980s is the launch of plastic catheters treated with silver or chlorhexidine, for use with hospitalized patients. Rigorous testing found these were proven to reduce incidences of catheter-related bloodstream infections (CRBSIs) in. Successes such as the above, as well as the rise of antibiotic-resistant bacteria in the early 2000s, helped these materials gain major adoption in the medical field, and led the way to the development of a new generation of operating room and hospital consumables.
Today, antimicrobial and disinfectant-compatible plastics are integral to a wide range of products, from smartphone cases to hospital surfaces, reflecting ongoing advancements in material science and public health priorities. A notable case study is the use of antimicrobial plastics in the keyboards and mice provided to hospitals by Seal Shield<, a leading manufacturer of infection control technology. Seal Shield’s products are designed to withstand frequent cleaning and disinfection, while effectively preventing microbial growth. This dual functionality not only extends the lifespan of the devices but also enhances patient safety by minimizing the risk of cross-contamination.
Types of Antimicrobial Agents Used in Plastics and Disinfectant-Compatible Plastics
Let’s look at some of the most commonly utilized methodologies for granting plastic materials antimicrobial and disinfectant-compatible properties.
Antimicrobial plastics
Antimicrobial plastics are engineered using various agents such as silver ions, triclosan, and copper-based compounds. Silver ions, one of the most commonly used antimicrobial agents, are highly effective against a wide range of microorganisms. They disrupt the cell membranes of bacteria, inhibiting their growth and reproduction. Triclosan, another widely used agent, targets bacterial enzymes and has been incorporated into numerous consumer products, though its use has become more controversial due to environmental and health concerns. Copper-based compounds, known for their broad-spectrum antimicrobial properties, are also popular in medical applications due to their efficacy and durability .
Disinfectant-compatible plastics
Disinfectant-compatible plastics are designed to withstand frequent exposure to cleaning agents without degrading. These plastics are essential in environments where rigorous hygiene is critical, such as hospitals and food processing facilities. Common disinfectants include alcohol, bleach, and quaternary ammonium compounds. Plastics that are compatible with these disinfectants typically feature enhanced chemical resistance, ensuring they maintain their integrity and antimicrobial properties even after repeated cleaning .
Antimicrobial disinfectant-compatible plastics - Use cases
While above we’ve specified for applications that require either antimicrobial or disinfectant-compatible plastics, in many real-world scenarios products require both properties in tandem. When planning your products be sure to challenge your manufacturing partners about the specific antimicrobial agents they use, how these agents are incorporated into the plastic, and their effectiveness against a range of microorganisms. Additionally, understand the compatibility of these materials with common disinfectants to ensure they can withstand regular cleaning without degrading.
A good case study demonstrating this are Teleflex Medical’s medical breathing circuits. These incorporate silver-based antimicrobial agents into their breathing circuits to reduce patients’ risk of ventilator-associated pneumonia, and are also designed to withstand regular disinfection with harsh cleaning agents. Clinical studies by the company and others have shown their devices lead to both better patient outcomes and reduced healthcare costs.
This is yet another example of how advancements in antimicrobial agents and disinfectant-compatible plastics are helping industry meet the growing demand for cleaner and more durable materials.
Selecting the Right Plastic for Your Product
As we’ve seen, the complexities of planning products that have antimicrobial and disinfectant-compatible properties arise, most often, from their desired use-cases. Often these products are meant for hospital and healthcare environments, and must therefore meet stringent compliance with regulatory standards.
#1 Evaluate your use-case
When selecting antimicrobial and disinfectant-compatible plastics for your products, several key factors should be considered to ensure optimal outcomes. First, assess the specific application and environment in which the product will be used:
- Medical devices – These settings require materials that not only inhibit microbial growth but also withstand repeated exposure to disinfectants without degrading. Availability of full manufacturers’ provenance for proof of compliance with regulatory requirements is a must.
- Consumer electronics – The focus for this sector is on durability and maintaining aesthetic appeal over time .
#2 What plastic material properties do you need?
Once you’ve evaluated the requirements of your use-case you can now review the properties of different antimicrobial agents and their compatibility with your desired plastics. Several widely used agents include:
- Silver ions offer broad-spectrum antimicrobial protection and are suitable for both medical and consumer products. However, they may be more expensive than other agents
- Triclosan has proven efficacy but has faced scrutiny and regulatory restrictions due to potential health and environmental impacts .
- Copper-based compounds provide durable and reliable antimicrobial properties, particularly for medical applications.
#3 Regulatory and safety considerations
Regulatory and safety considerations are crucial in the selection process. Ensure that the materials comply with relevant standards and guidelines set by authorities such as the FDA, EPA, and REACH. For example, the FDA provides guidelines for antimicrobial additives in medical devices, emphasizing the need for thorough testing to demonstrate safety and efficacy . Additionally, consider any industry-specific certifications that might be required, such as ISO standards for medical devices.
A good example for a company that released a product that successfully navigated the choices and challenges above are 3M, with their development of antimicrobial surgical drapes. 3M’s drapes are designed to withstand hospital grade sterilization processes, and incorporate iodine-based antimicrobial agents to help combat infection and keep operating environments germ-free. The drapes are FDA certified and have been shown to significantly reduce surgical site infections. 3M has grown to be the largest single provider of this class of products and controls 11% of the global market. This case study showcases how selecting appropriate and compliant materials helps reach commercial success .
#4 Selecting the Right Plastic Parts Factory for Your Product
Once you have a clear understanding of your product and the materials it requires, you can start your search for a manufacturing partner. When engaging with potential suppliers, ask detailed questions about their materials and manufacturing processes. Selecting the right OEM supplier for antimicrobial and disinfectant-compatible plastic parts is crucial for ensuring product quality and compliance:
- Certifications – Look for suppliers who meet the regulatory requirements and industry standards your product will need to get certified. These are typically specific ISO certifications (see the appendix), but there may be additional requirements as well.
- Quality control – Check your supplier candidates to ensure they have robust quality control processes in place to maintain the consistency and safety of your products.
Antimicrobial and Disinfectant-Compatible Plastics - Conclusion
In summary, due to antimicrobial and disinfectant-compatible plastics’ propensity to help reduce microbial contamination and enhance product safety and longevity, the demand for products incorporating these plastics is expected to keep rising, particularly in the consumer electronics and medical device industries.
To utilize these plastics effectively product managers must consider the specific use-case and environment, and also review any regulatory compliance requirements that may be applicable.
For medical devices, it’s important to prioritize materials that can withstand frequent disinfection and comply with stringent regulatory standards like FDA and ISO. For consumer electronics the focus is more on durability and maintaining aesthetic appeal. Understanding the properties of different antimicrobial agents—such as silver ions, triclosan, and copper-based compounds— helps select the best material for your product.
Selecting the right OEM supplier is also vital – For professional advice and an in depth review of your product brief, feel free to reach out to us here at Alcamiglobal.com. We have a proven track record working as an OEM for some of the world’s most stringent and exacting manufacturers (e.g. Dyson, Western Digital, Stanley Black & Decker, etc.), and our managing director, Mr. Kris Withouck, is always happy to review your product plans for a consultation. We look forward to your call!
Photo by Mockup Graphics on Unsplash
Get in Touch - We Can Help
Alcami combines different production technologies allowing us to provide a turnkey solution for a variety of parts. We combine this with sourcing and logistics services, so our customers don’t need to worry about shipping and storage.