- © 2025 Alcami Manufacturing (Thailand) Co., Ltd. All rights reserved
- Privacy Policy
News
Food-Safe Plastic Thermoforming – A Practical Guide
This guide provides a practical overview for engineers and professionals in the food industry focusing on food-safe plastic thermoforming. Understanding these processes is crucial for ensuring food safety and compliance with industry regulations. In the following sections, we’ll explore key aspects of plastic thermoforming, outlining how adherence to certain practices benefits the food industry. The goal is to equip industry professionals with the knowledge to make informed decisions in their thermoforming applications.
Get in touch...
No matter what your manufacturing project, Alcami is here to help. We have an in-house team of design engineers and incorporated post-production services to help us run your project smoothly from start to finish. Contact us today to learn more about what we can do for you.
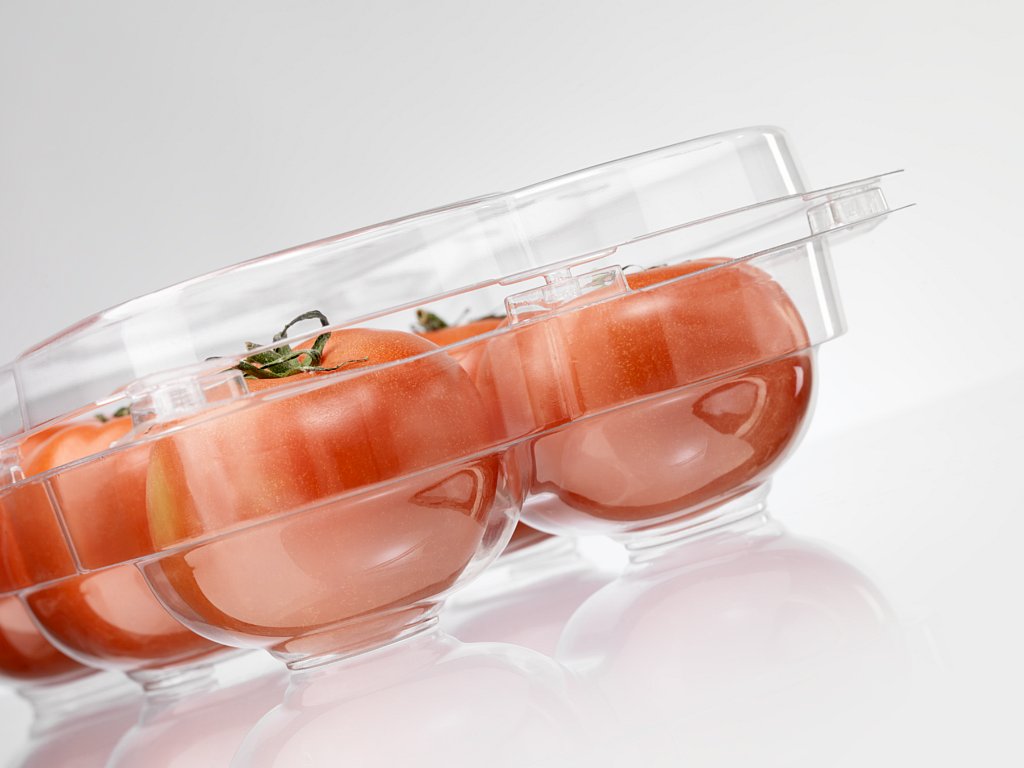
Ensuring food-safe Practices in Plastic Thermoforming
Food safety remains a cornerstone concern in the food industry. For plastic thermoforming manufacturers, the use of food-grade materials is not just a best practice but a regulatory requirement. Adhering to FDA regulations in the United States or EFSA standards in Europe ensures the elimination of potential harmful substance contamination in food products. A notable example is the incorporation of PET (Polyethylene Terephthalate) in thermoforming. This material is not only safe for food contact but also boasts significant recyclability, aligning with environmental goals. FDA Guidelines on Food-Grade Materials and EFSA Standards provide detailed insights into these regulations.
A generalized case study highlighting the effectiveness of these practices can be found in the implementation of PET in beverage packaging. Major beverage companies have successfully transitioned to PET packaging, as documented in reports and studies available on resources like Packaging Digest and Beverage Industry Magazine. These sources illustrate how adopting food-safe plastics not only meets regulatory compliance but also enhances consumer trust and marketability.
By selecting manufacturers that rigorously follow these food safety standards, companies in the food industry can assure that their packaging aligns with safety requirements, thereby safeguarding consumer health and meeting legal obligations. This practice is not only essential for compliance but also for maintaining a strong reputation in the highly competitive food market, where safety and quality are paramount.
Quality Control in Plastic Thermoforming
Quality control is a fundamental aspect of ensuring food-safe plastic thermoforming products. The implementation of rigorous quality control systems not only guarantees the consistency and reliability of product quality but also reflects a manufacturer’s dedication to excellence. Achieving certifications like ISO 22000, which is focused on food safety management, is a clear indicator of this commitment. For detailed information on ISO 22000 standards, ISO’s official website offers comprehensive insights.
A generalized case study demonstrating the impact of such quality standards can be seen in the food packaging sector. Companies that have achieved ISO 22000 certification often report significantly fewer defects and higher customer satisfaction, as evidenced by a study from the American Society for Quality (ASQ). More information on these findings can be accessed through the ASQ website. This certification not only ensures adherence to safety standards but also positions a company as a reliable partner in the food industry.
By collaborating with manufacturers who prioritize these certifications, professionals in the food industry can secure a consistent supply of high-quality, food-safe plastic thermoforming packaging. This approach not only minimizes the risk of product recalls but also bolsters the brand’s reputation in the market, ensuring compliance with industry regulations and customer expectations.
Material Compliance in Food-Safe Plastic Thermoforming
Selecting suitable materials for thermoforming is a critical step in ensuring the safety and functionality of food packaging. These materials must adhere to food contact regulations and be appropriate for their intended use. Polystyrene, known for its versatility and cost-effectiveness, is a common choice in the production of disposable food containers. Resources like the FDA’s guide on food contact substances provide comprehensive guidelines on material compliance for food contact.
A case study illustrating this point can be found in the fast-food industry. Major fast-food chains have shifted to polystyrene containers for certain food products due to its suitability for both hot and cold foods, a transition documented in industry reports available on Food Packaging Forum. However, the material’s ability to withstand microwave or freezer conditions is also a crucial consideration, as not all materials are suitable for such extremes.
By carefully selecting materials that meet both regulatory standards and practical needs, manufacturers can deliver plastic thermoforming solutions that ensure food safety, durability, and consumer convenience. This approach not only complies with industry regulations but also caters to the varying demands of food products, ensuring a versatile and effective packaging solution.
Advancing Sustainability in Plastic Thermoforming for the Food Industry
The role of sustainability in plastic thermoforming, particularly in the context of the food industry, is becoming increasingly crucial. Utilizing recyclable materials like PET not only minimizes environmental impact but also resonates with the growing consumer demand for eco-friendly packaging. The Environmental Protection Agency (EPA) has reported an uptick in recycling rates for PET packaging, indicative of the shift towards more sustainable practices in the industry. EPA’s report on PET recycling provides insights into this trend.
A relevant case study in this arena is the beverage industry’s move towards PET bottles. Major beverage manufacturers have adopted PET for its recyclability and reduced carbon footprint, as seen in industry analyses available on Beverage Industry Magazine. This shift not only aligns with environmental goals but also enhances brand perception among environmentally conscious consumers.
By embracing sustainable thermoforming processes, manufacturers in the food industry can significantly contribute to environmental protection while meeting the expectations of eco-conscious consumers. This commitment to sustainability is a key factor in aligning with the contemporary market trends and maintaining a competitive edge.
Enhancing Product Appeal through Customized Plastic Thermoforming
Plastic Thermoforming
Customization in plastic thermoforming is a significant factor in tailoring packaging to meet specific industry requirements. This flexibility allows for the creation of unique packaging shapes, sizes, and features, enhancing functionality and aesthetic appeal. The Packaging Machinery Manufacturers Institute (PMMI) has highlighted in its study that customization in packaging can substantially increase consumer engagement and drive sales, as detailed on PMMI’s website.
A practical example of this is observed in specialty food markets, where customized packaging has been instrumental in differentiating products on crowded shelves. Reports on this trend can be found through resources like Packaging World. By utilizing these customization capabilities, professionals in the food industry can create distinctive packaging that not only captures consumer attention but also meets specific functional requirements, thereby adding significant value to their products.
Adopting such tailored solutions in plastic thermoforming not only meets the stringent requirements for food safety but also significantly elevates the consumer appeal of products, contributing to a stronger market presence.
Ensuring Compliance and Building Trust with Proper Labeling in Plastic Thermoforming
In the realm of plastic thermoforming for food packaging, the importance of accurate and compliant labeling cannot be overstated. It is crucial for labels to provide clear and precise information about the material, recycling instructions, and other relevant data, in line with regulatory standards. The Food Safety and Inspection Service (FSIS) emphasizes the impact of proper labeling on consumer trust. Their survey results, which can be accessed on FSIS’s website, demonstrate how accurate labeling significantly bolsters consumer confidence in product safety and quality.
An illustrative case study in this area is the implementation of clear labeling practices in the dairy industry. The transition to more transparent labeling, as reported in industry journals such as Dairy Foods Magazine, has not only ensured regulatory compliance but also enhanced consumer trust and loyalty. By adhering to stringent labeling standards, food packaging companies can fulfill legal obligations and, more importantly, reinforce consumer trust in the safety and quality of their products.
This approach is vital in maintaining a strong, trustworthy brand presence in the competitive food industry, especially in sectors that rely heavily on the safety and quality of plastic thermoformed packaging.
Maximizing Safety and Efficiency with Traceability
Implementing robust traceability systems in plastic thermoforming is a critical factor in ensuring the safety and efficiency of the production process. These systems enable the tracking of packaging production and distribution, which is essential for quality control and vital in situations like product recalls. A prominent example of traceability playing a crucial role can be seen in the food industry, where such systems have swiftly addressed contamination issues, thereby minimizing consumer impact and protecting brand reputation. For more insights into traceability implementation see Food Safety Magazine.
Effective traceability in plastic thermoforming not only ensures transparency throughout the production process but also facilitates rapid response to any quality concerns. This approach is indispensable in maintaining high standards of food safety and upholding consumer trust in the food industry, particularly where plastic thermoformed packaging is used.
Driving Growth with Technological Innovations in Plastic Thermoforming
In the rapidly evolving sector of plastic thermoforming, staying abreast of technological advancements is not just beneficial; it’s a necessity for maintaining a competitive edge. The incorporation of cutting-edge technologies like 3D printing and automation has revolutionized the thermoforming process, leading to more efficient and precise production. A detailed case study by the Society of Manufacturing Engineers (SME), available on their website, showcases how a food packaging company achieved a remarkable 30% increase in production efficiency by integrating these advanced technologies.
Further reinforcing this trend, research and reports from industry platforms like Plastics Technology highlight similar advancements in the field. By adopting these innovative techniques, manufacturers in the plastic thermoforming industry can not only streamline their production processes but also offer superior solutions that meet the rigorous standards of food safety. Such proactive adoption of technology plays a pivotal role in enhancing the overall market position of these manufacturers.
Optimizing Supply Chain Management in Food-Safe Plastic Thermoforming
A robust and efficient supply chain is a cornerstone in the plastic thermoforming industry, especially when catering to the fast-paced demands of the food sector. The necessity for rapid turnaround and high-volume production makes supply chain management a pivotal aspect. The National Association of Manufacturers (NAM) emphasizes this in their report, highlighting how supply chain efficiency is intrinsically linked to a company’s market responsiveness. This report and further information can be found on NAM’s website.
A case in point is the implementation of just-in-time (JIT) inventory strategies in the food packaging sector. Companies utilizing JIT, as documented in studies available on Supply Chain Management Review, have seen improvements in production efficiency and inventory management. By refining supply chain processes, manufacturers in the plastic thermoforming industry can ensure the prompt delivery of high-quality, food-safe products, thereby reinforcing their standing in a competitive market.
Final Thoughts on Advancing Food Safety and Efficiency in Plastic Thermoforming
Plastic thermoforming is integral to the food industry, playing a pivotal role in ensuring food safety and maintaining high standards of packaging quality. By adhering to the practices outlined here, professionals in this sector can provide packaging solutions that are not only safe and compliant but also highly effective. The importance of these practices extends beyond just consumer health; they also contribute significantly to environmental sustainability, operational efficiency, and the strengthening of brand reputation.
Continued advancements demonstrate the industry’s commitment to innovation and adaptation. As the sector evolves, staying informed and flexible in adopting these best practices will remain crucial for future success. Embracing the dynamics of food-safe plastic thermoforming will undoubtedly position companies for enduring success in this competitive landscape.
Here at Alcami we offer food-safe plastic thermoforming in a cleanroom environment. We look forward to your inquiries!
Get in Touch - We Can Help
Alcami combines different production technologies allowing us to provide a turnkey solution for a variety of parts. We combine this with sourcing and logistics services, so our customers don’t need to worry about shipping and storage.