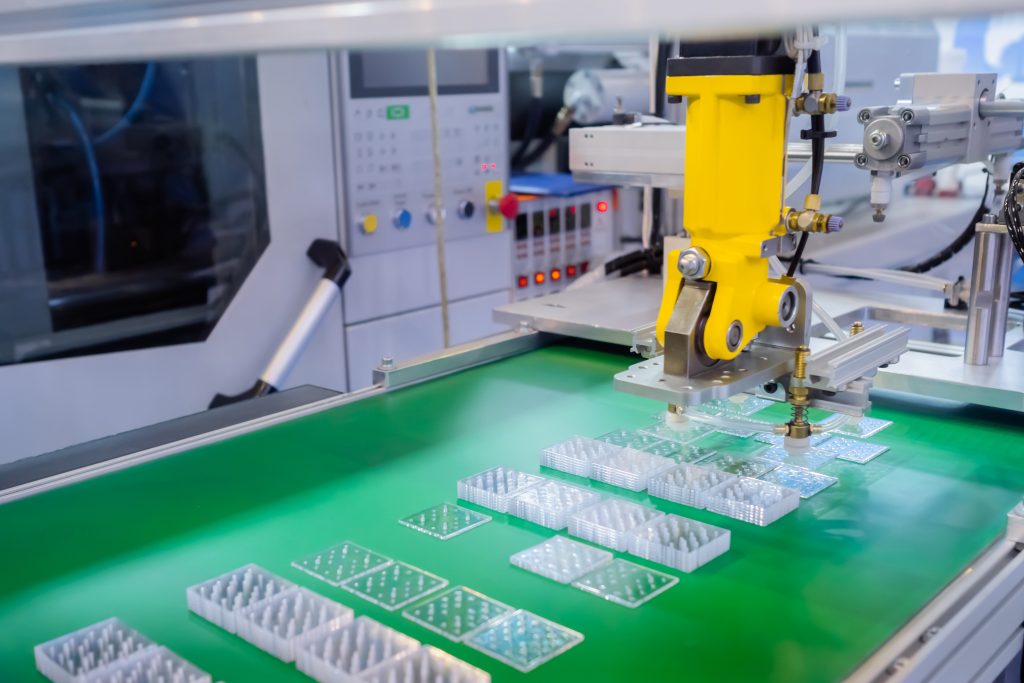
Automation Tray
One of our customers has been investing in automation equipment to automate their production line. This automation will increase their output with 20%, using less operators.
Plastic injection molding is a cornerstone of Alcami Global’s production capabilities, offering unparalleled precision and efficiency for creating high-quality plastic parts.
By injecting heated materials into custom molds, this process produces single-piece parts that are strong, consistent, and perfectly replicable. It’s the preferred solution for industries seeking reliable, scalable, and cost-effective manufacturing.
This technology is ideal for maintaining part consistency and reliability. The process is not only efficient for high-volume production but also highly cost-effective, ensuring you get the best value for your investment.
A diverse range of plastic materials can be used to create parts across many different industries, furthermore Alcami has earned ISO 9001, 14001,& 22000 certifications & offers cleanroom production capabilities that meet all the requirements for food-safe, electronics and medical grade parts:
We’re eager to manufacture for you according to your exacting compliance requirements.
At Alcami we can advise you through every step of your production process:
Alcami engineers are available to assist in realizing any of your project ideas. We offer expert Mold Design consultation and a variety of mold fabrication options, providing you with a turnkey solution for all your production needs.
Every cycle of the injection molding process for each part manufactured has several steps:
MOQs are variable by the scope and complexity of the parts you need manufactured. Volumes for checkout-point toys, are obviously higher than those for electronic device casings… 🙂
We evaluate projects on a case-by-case basis, so please talk to us today to share the details of your project.
The replicability of the technology means that it is an excellent way to manufacture identical parts in high volumes. The largest costs incurred are during the beginning stages of production when designing and fabricating your mold. After this, the cost per part produced is very low.
This makes injection molding ideal for…
The injection molding process is a highly sustainable process, which results in very little post-production scrap. Even the small amount of leftover plastic from injection molding can typically be reground and recycled in future processes. As an ISO 14001 certified company, Alcami is dedicated to reducing its environmental footprint and promoting sustainability and efficiency throughout all its production processes.
The injection molding process creates single-piece parts of a uniform material, which gives them considerable strength and high levels of product consistency. This allows a high level of detail to be imprinted on parts, which have exceptional color control and an attractive finish immediately upon ejection. This makes injection molding ideal for:
Ready to transform your project with expert plastic injection molding? Contact us for customized solutions that deliver precision, quality, and efficiency. Our engineering team is eager to collaborate with you and meet your unique production requirements.
Allow us to help you tackle any injection molding project with precision, creativity and competitive pricing.
At Alcami we advise you through every step of your production process. If you choose injection molding for your project, there are a few stages of production that we will guide you through:
Alcami can help provide you with engineering assistance to bring to life your Mold Design ideas or provide the knowledge and expertise to counsel your internal engineers on creating operable designs for Alcami machines.
We offer expert design consultation and a variety of mold fabrication options, providing you with a turnkey solution for all your production needs.
Injection molding can be done with a wide variety of materials, including plastics, metals, glasses, and elastomer materials. Alcami most frequently uses the following materials in its projects.
In addition to commonly used injection molding material options, Alcami strives to offer and promote sustainable materials such as bio-based, biodegradable, and recyclable plastics. We are on the cutting edge of sustainable manufacturing practices and are dedicated to ensuring that our work supports a healthier planet.
Whatever your injection molding project, our engineering team can help you look at the best material options and design strategies to provide you with the highest quality product possible.
As the most common production method for plastic parts, injection molding has a diverse array of applications:
Let us know if you are interested in an application not listed here. Our engineers are happy to advise you on how to use injection molding to complete your project with flexibility and quality assurance.
Alcami is dedicated to the highest level of quality assurance in all of our production work. As an ISO 9001 certified company, cleanroom production is an essential part of our guarantee to provide optimal sanitation and quality standards for any project. We are able to certify quality and cleanliness in manufacturing parts for a wide range of industries, including…
The Alcami group has several facilities in Thailand, including manufacturing and packaging locations.
The Alcami group has several facilities in Thailand, including manufacturing and packaging locations.
Explore our latest news, research, and insights.
One of our customers has been investing in automation equipment to automate their production line. This automation will increase their output with 20%, using less operators.
One of our customers is a multinational company which is in white goods, meaning washing machines, refrigerators, ovens, stoves, etc.
Established and patented in 2004, the Scraperite brand is a line of plastic razor blades and holders developed for cleaning and scraping on surfaces where metal scrapers and blades would cause damage.
One of our customers has been investing in automation equipment to automate their production line. This automation will increase their output with 20%, using less operators.
One of our customers is a multinational company which is in white goods, meaning washing machines, refrigerators, ovens, stoves, etc.
Established and patented in 2004, the Scraperite brand is a line of plastic razor blades and holders developed for cleaning and scraping on surfaces where metal scrapers and blades would cause damage.
Alcami combines different production technologies allowing us to provide a turnkey solution for a variety of parts. We combine this with sourcing and logistics services, so our customers don’t need to worry about shipping and storage.