News
An Introduction to Working with Radio Frequency Embedded Plastics
A Brief History of Radio Frequency Embedded Plastics
The integration of Radio Frequency (RF) technology into plastics began in the mid-20th century, focusing initially on military and aerospace applications. The first major milestone was the introduction of RFID (Radio Frequency Identification) technology in the 1970s, primarily for tracking and inventory management. This demonstrated the potential of RF embedded plastics across various industries.
In the 1980s, the medical field began using RF embedded plastics in devices like RFID wristbands for patient identification, improving safety and workflow efficiency. The 1990s saw the expansion into consumer electronics, with mobile phones and wireless networking equipment incorporating RF components in plastic housings, showcasing their versatility.
In the early 2000s use of RF embedded plastics in automotive keyless entry systems demonstrated their durability in demanding environments.
Get in touch...
No matter what your manufacturing project, Alcami is here to help. We have an in-house team of design engineers and incorporated post-production services to help us run your project smoothly from start to finish. Contact us today to learn more about what we can do for you.
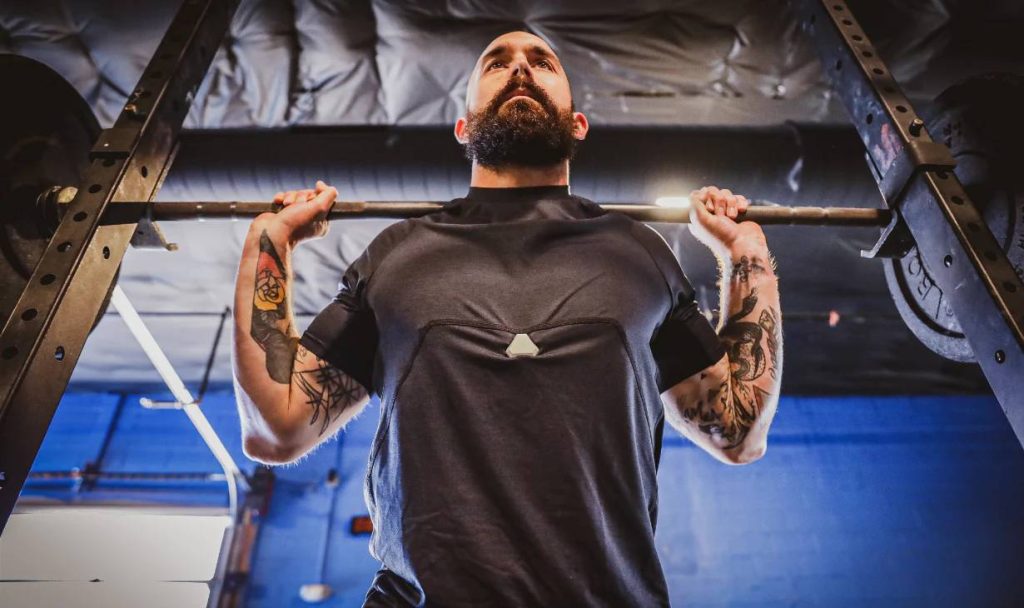
Contemporary RF Technology Applications
Nowadays, RF technology is widely used across sectors and industries. A few examples would be the use of RF in consumer electronics devices that connect wirelessly to other devices and networks – devices such as smartphones, tablets, and wireless routers. RF technology is also widely utilized in the medical field for diagnostic equipment, such as MRI machines, and for RF identification (RFID) systems, which track and manage medical supplies and patient information.
RF technology is also applied in the automotive industry, where it is used for keyless entry systems and tire pressure monitoring systems (TPMS). These systems improve vehicle security and safety by allowing remote access and real-time monitoring of tire conditions.
The prevalence of RF embedded plastics in industry continues to grow. The global radio frequency identification (RFID) market was worth USD 15.8 billion in 2023, and is projected to reach USD 40.9 billion by 2032.
Future Trends
Key Benefits of RF Embedded Plastics
Working With RF Embedded Plastics - Materials and Processes
Radio frequency (RF) embedded plastics integrate RF technology into plastic components, enhancing their functionality for various applications. Common plastics chosen for RF embedding processes include:
- Polyethylene (PE)
- Polypropylene (PP)
- Polycarbonate (PC)
The above are preferred for their durability, flexibility, and compatibility.
The manufacturing process typically involves injection molding, which provides design flexibility, high quality finishing, and affordability for large scale production. During the injection process the plastic is melted and pushed (injected) into a mold containing the RF component. Small scale manufacturing can utilize 3D printing for prototyping and limited production runs.
Challenges in manufacturing RF embedded plastics include ensuring the RF components’ stability during the molding or printing process, and maintaining the plastic’s structural integrity. For example, in injection molding, high temperatures can damage RF components if not properly managed. Best practices to address these challenges include using temperature-resistant RF components and optimizing mold design to distribute heat evenly.
Product Managers’ Considerations - Design and Integration
When designing products with RF embedded plastics, several factors must be considered. RF components must be strategically placed to ensure optimal performance, avoid interference with other electronic parts, and ensure accurate signal transmission.
Product managers should also focus on the compatibility of RF components with the chosen plastic material. Different plastics have varying dielectric properties, which can affect the performance of RF components. Collaboration with materials scientists and engineers is essential to select the appropriate plastic and ensure seamless integration.
Product Managers’ Considerations - Regulatory and Compliance Requirements
Regulatory compliance is critical in industries such as medical devices and consumer electronics. Product managers must ensure that RF embedded plastic products comply with relevant regulations, such as those set by the Federal Communications Commission (FCC) for electronic devices and the Food and Drug Administration (FDA) for medical devices. These regulations often involve rigorous testing to verify that the RF components do not interfere with other devices and that the product is safe for use.
Compliance with international standards, such as ISO 13485 for medical devices, is also important for market acceptance. Product managers should work closely with compliance experts to navigate these regulatory requirements and ensure that their products meet all necessary standards.
Which Plastic Factory to Work With?
Choosing the right plastic OEM factory is crucial for the successful production of RF embedded plastics. Criteria for selection should include the supplier’s experience with RF technology, quality control processes, and ability to meet regulatory requirements. It’s essential to conduct thorough evaluations of potential suppliers, including site visits and audits, to ensure they have the capabilities to produce high-quality RF embedded plastic parts.
Collaboration with suppliers during the design and development phases usually leads to better RF component integration, and more efficient manufacturing processes. Our own experiences working on the wearable fitness and health devices developed by Notch Ltd. provided ample examples of this – By choosing to bring us into the design process early on, the Notch team were able to rely on us for help with improvements to their products’ waterproofing, electronic components conductivity, and sensors’ performance.
Conclusion - RF embedded plastics enhance functionality
RF embedded plastics enhance functionality, improve safety and security, and offer cost efficiency. Integrating radio frequency (RF) technology into your plastics products offers significant advantages and benefits that make them a good choice for those seeking innovative solutions.
To be successful when working with RF embedded plastics, it is crucial to understand the materials and processes involved, as well as the challenges that might arise during manufacturing. The complexity of these projects makes choosing the right materials and manufacturing methods especially important, as it can mitigate potential issues. Partnering with a proven and reliable OEM supplier is essential.
Here at Alcamiglobal.com we welcome product managers, plastic engineers, and entrepreneurs interested in exploring RF embedded plastic product development. We have a proven track record working as an OEM for some of the world’s most stringent and exacting manufacturers (e.g. Dyson, Western Digital, Stanley Black & Decker, etc.) Our founder, Mr. Kris Withouck, is always happy to offer his expertise and provide initial manufacturing feedback. His extensive experience and knowledge can help you navigate the complexities of getting your products manufactured with optimal results. Leverage our expertise to stay ahead of the curve and deliver innovative, high-quality products to your customers. Contact us today.
Get in Touch - We Can Help
Alcami combines different production technologies allowing us to provide a turnkey solution for a variety of parts. We combine this with sourcing and logistics services, so our customers don’t need to worry about shipping and storage.