Scraperite
Established and patented in 2004, the Scraperite brand is a line of plastic razor blades and holders developed for cleaning and scraping on surfaces where metal scrapers and blades would cause damage. Blades are offered in varying compositions to suit combinations of solvent, substance, and surfaces. These products are commonly referred to as safety scrapers and used in professional industry as well as for general consumer use. The products are currently used in various sectors and geographies around the world, from aerospace to zoo keepers.
In 2019 the company implemented a rebranding and repositioning strategy, including full product and packaging redesign. Developing new products with new packaging requires a full restart from scratch. It’s a detailed and tedious process with many challenges along the way, so finding a partner who can dedicate time and focus to resolve problems and devise accommodating solutions is paramount. After careful consideration, Scraperite selected to work with the team at Alcami Manufacturing (Thailand) Co., Ltd.
Get in touch
No matter what your manufacturing project, Alacami is here to help. We have an in-house team of design engineers and incorporated post-production services to help us run your project smoothly from start to finish. Contact us today to learn more about what we can do for you.
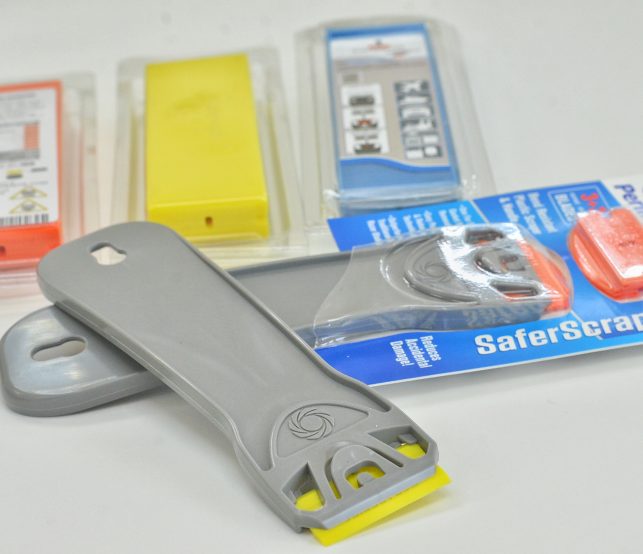
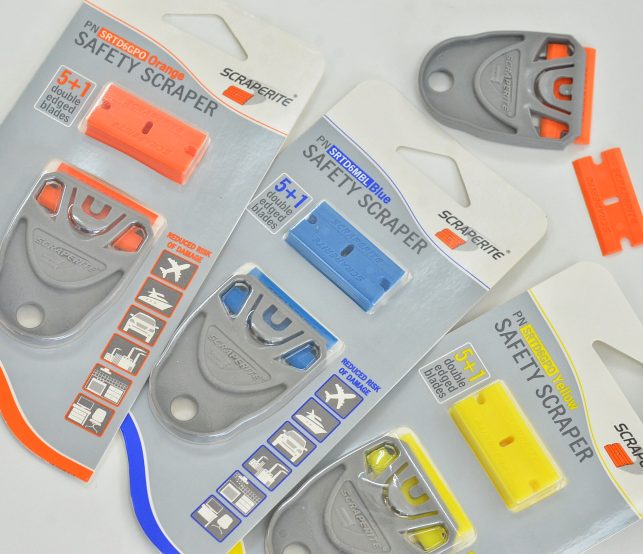
Scraperite Objectives
- Redesign the product line to include newly patented features
- Implement a new business model to include sustainability programs
Move production completely out of China
Timeline
Overall initial project portion yielded seven products over the course of one year and has become an ongoing project as new products are introduced.
- Product design refinements: 6 weeks
- Prototyping: 4 weeks
- Molds: 6 weeks
- Packaging design and refinement: 12 weeks
- Production and delivery: 6 weeks
- First product delivery: 34 weeks
Communication and Skills
Clear communication is a key element to any successful association. Alcami’s team of more than 100 staff is able to communicate in French, English, and Thai languages and offers talent skills including extensive material knowledge, engineering, and process control.
The extensive resources of CNC machines, clean rooms, and large factory footprint gives them an ability to offer many solutions in-house, which allowed Scraperite to achieve rapid success in the rebranding and product launch.
Product design and Production
The thorough and standardized process established by Alcami allows them to engage at every step starting from the early stages of hand sketches onward to a finished palletized product. Each product handled separately, moving from sketch to computer aided design (CAD) renderings in order to create prototype molds.
This is an important distinction from 3D printing since actual production materials can be tested in real use situations. After design and materials are clearly aligned, production molds are developed using a smart rotary layout for faster cycle time and product output, yielding reduced costs.
Recyclable Packaging
Packaging design and refinement are just as tedious in process and creation. Some outsourced portions like design and printing become an added management element, including accurate material selection, colors, size, delivery timelines, and more. Each requiring quality control before assembly can begin. Working through many trials and tribulations in the early stages, Alcami now successfully manages every detail to maintain a fluid process.
Scraperite requires fully recyclable packaging which means the plastic and cardboard portions must remain separate. This trapped blister format places the plastic blister portion, sandwiched but floating, between two sheets of thin cardboard glued together. This ensures a clean presentation with solid construction with each portion separating cleanly to make it fully recyclable. Again, requiring several tests and refinements to get it right.
Scraperite and Alcami decided on another important packaging distinction by using polyethylene terephthalate (PET) for the blister portion, making it truly recyclable. Same as a water bottle. Unlike most commonly used polyvinylchloride (PVC) blister material which is less recycling friendly. To compound the problem, these PVC blisters are typically glued to the face of the cardboard which makes that portion unrecyclable.
Scraperite takes recycling concerns one step further by implementing a pack design where used blades can be reinserted in the pack. The packaging outer shell uses PET material with a dual compartment setup internally where new blades come from one side while the used blades are inserted in the other end.
Alcami developed a clever production feature to accommodate this design feature by including a small third part that slides to create just the right amount of separation between used and fresh product. These packs are taken back by Scraperite for correct recycling, closing the plastic use loop by bringing everything back for correct recycling and re-use in the production of other products.
Assembly, Quality Control, and Delivery
After all the above is refined and defined, packaging and preparation for final delivery is also handled by Alcami, including outer box sourcing and printing for each product. This assures quality of control from unit level onward through correct labeling and palletizing, all to deliver a full turnkey solution for Scraperite.
Overall Result
- Scraperite successfully transitioned out of China, effectively ceasing operations from one order to the next
- More effective communication has yielded more attention to detail in product refinement for an overall better user experience for Scraperite buyers
- Faster turnaround times using structured process control ensures better quality control than ever before
- Enabled important Scraperite sustainability programs including product and packaging recycling characteristics and replacement warranty on holders – programs designed to keep Scraperite products out of landfills and oceans
Get in Touch - We Can Help
Alcami combines different production technologies allowing us to provide a turnkey solution for a variety of parts. We combine this with sourcing and logistics services, so our customers don’t need to worry about shipping and storage.