- © 2025 Alcami Manufacturing (Thailand) Co., Ltd. All rights reserved
- Privacy Policy
News
Injection Molding & Cleanroom Practices: A Comprehensive Guide for the Medical Business
Introduction to Injection Molding
Welcome to the fascinating world of injection molding, a manufacturing marvel that has revolutionized the production of plastic parts. This process, known for its versatility and reliability, is a cornerstone in mass-manufacturing, capable of creating parts in large volumes with remarkable consistency.
Imagine a process where molten plastic is injected into a mold, then cooled to form a solid part. Now, imagine this process repeating thousands, even millions of times, each cycle producing a part identical to the last. That’s the magic of injection molding.
But where does this process shine the brightest? In the medical sector. Here, the stakes are high, and the need for precision, sterility, and consistency is paramount. From surgical instruments to implantable devices, injection molding is the silent hero behind the scenes, making it all possible.
So, let’s embark on this journey together, exploring the role of injection molding in the medical business, the importance of cleanroom standards, and the exciting future trends in this field. We’ll also give you a glimpse into our capabilities at Alcami, where we’re pushing the boundaries of what’s possible with injection molding. Let’s dive in!
Get in touch
No matter what your manufacturing project, Alcami is here to help. We have an in-house team of design engineers and incorporated post-production services to help us run your project smoothly from start to finish. Contact us today to learn more about what we can do for you.
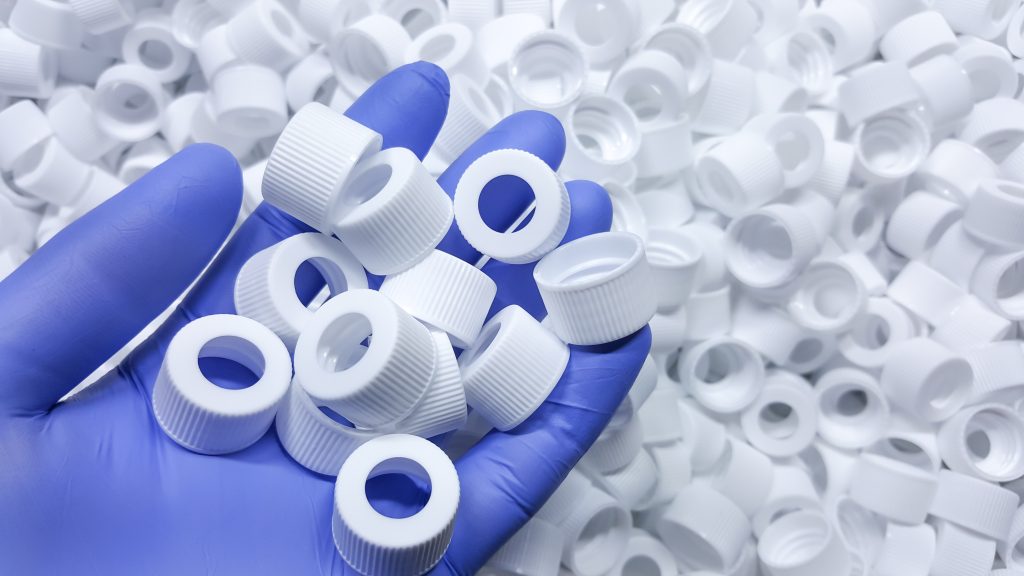
The Role of Injection Molding in the Medical Business
Injection molding plays a crucial role in the medical industry. It’s instrumental in producing a wide range of components, from surgical instruments to implantable devices. The ability to create intricate, high-precision parts that meet the stringent standards of the medical field is a significant advantage of Mould Injection Moulding.
. Moreover, the use of plastics in injection molding, known for their flexibility, durability, and resistance to bacteria, makes it an ideal choice for medical applications.
Cleanroom Standards in Injection Molding
Cleanrooms are integral to the injection molding process. They are environments with a controlled level of contamination, defined by the number of particles per cubic meter at a predetermined molecule measure. Cleanrooms are used in various industries, including microelectronics, biology, nuclear work, and pharmaceutics.
At Alcami, we utilize an ISO 7 cleanroom for our injection molding processes. This standard ensures that there are no more than 352,000 particles (0.5 microns or larger) per cubic meter of air. This level of cleanliness is crucial in preventing contamination during the production process.
Benefits of Cleanroom Injection Molding
Cleanroom injection molding offers numerous benefits, especially in the medical industry where the highest standards of cleanliness and precision are required. Here are some key advantages:
- Reduced Contamination: Cleanrooms maintain low levels of particulates, significantly reducing the risk of product contamination – a crucial factor for medical devices.
- Increased Product Quality: The controlled environment of a cleanroom ensures consistent conditions for production, leading to higher product quality and lower product rejection rates.
- Improved Compliance: Cleanroom injection molding can help manufacturers meet stringent regulatory standards related to manufacturing environments.
- Enhanced Reputation: Using a cleanroom for injection molding can boost a company’s reputation, demonstrating a commitment to quality and safety.
- Greater Precision and Consistency: The controlled conditions within a cleanroom can lead to greater precision and consistency in the molding process, which is particularly important for medical devices.
- Safe Environment for Workers: Cleanrooms are designed to be safe environments for workers, with good ventilation and minimized risk of exposure to harmful substances.
Alcami’s Capabilities in Injection Molding
At Alcami, we use medical-grade plastics for our injection molding processes. These materials are biocompatible, durable, and resistant to various sterilization methods. Our molded parts adhere to tight tolerances, ensuring high-quality and consistency in every product.
Safety is a top priority in our operations. Our team follows strict protocols when working in the cleanroom, including wearing appropriate personal protective equipment and adhering to rigorous cleaning procedures.
We have a comprehensive process to prevent contamination. This includes regular cleaning and maintenance of the cleanroom, strict personnel protocols, and the use of High-Efficiency Particulate Air (HEPA) filters to remove particulates from the air.
Quality control is integral to our operations. We monitor the quality of our molded parts through various methods, including visual inspection, dimensional analysis, and functional testing.
Future Trends in Injection Molding
The future of injection molding in the medical business is promising. With advancements in technology, we anticipate further improvements in precision, efficiency, and material capabilities. Here are some key trends to watch:
- Internet of Things (IoT): The IoT allows for real-time monitoring and control of the injection molding process. Sensors can collect data on various parameters, which can be analyzed to optimize the process, improve consistency, and reduce defects.
- Advanced Materials: The development of new, medical-grade plastics will expand the possibilities of injection molding, enabling the creation of more complex and innovative medical devices.
- 3D Printing: While 3D printing is not set to replace injection molding, it’s a complementary technology that can be used for rapid prototyping, reducing the time and cost to bring a new product to market.
- Sustainability: As the medical industry seeks to reduce its environmental impact, we anticipate a greater focus on sustainability in injection molding. This could include the use of bio-based or recyclable plastics, energy-efficient machinery, and processes that minimize waste.
Conclusion
In conclusion, the intersection of injection molding and cleanroom practices is a powerful combination that offers immense benefits for the medical business. The ability to produce high-quality, reliable, and safe medical components in a controlled environment is a testament to the advancements in this field.
At Alcami, we are not just keeping pace with these advancements; we are at the forefront, driving innovation. We are committed to leveraging cutting-edge technology and best practices to ensure the highest standards in our products. Our use of medical-grade plastics, adherence to cleanroom standards, and rigorous quality control measures are all part of our commitment to excellence.
Looking ahead, the future of injection molding in the medical business is bright. The integration of IoT and other emerging technologies promises to bring about even greater precision, efficiency, and capabilities. The development of advanced materials will open up new possibilities for medical devices, while a focus on sustainability will ensure that progress does not come at the expense of our planet.
As we navigate this exciting future, we remain guided by our mission to deliver high-quality, reliable, and safe medical components. We are excited about the opportunities that lie ahead and are committed to continuing to serve our customers with the highest standards of quality and safety.
Here at Alcami we offer medical grade platic injection in a cleanroom environment. We look forward to your inquiries!
References
- International Organization for Standardization. (n.d.). ISO 14644-1:2015 – Cleanrooms and associated controlled environments — Part 1: Classification of air cleanliness by particle concentration. Link
- ISO. (2015). ISO 14644-1:2015 Cleanrooms and associated controlled environments — Part 2: Specifications for testing and monitoring to prove continued compliance with ISO 14644-1. Link
- Plastics Today. (n.d.). Medical Plastics 101. Link
- Mecart Cleanrooms. (n.d.). Cleanroom Classifications (ISO 8, ISO 7, ISO 6, ISO 5). Link
- 3D Insider. (n.d.). Injection Molding: What It Is, How It Works, Who Is It For. Link
- The Rodon Group. (n.d.). The Evolution of Plastic Injection Molding What’s Next.
- MarketsandMarkets. (n.d.). Cleanroom Technology Market by Product (HVAC, HEPA Filters, Air Shower, Air Diffuser), Construction (Hardwall, Softwall), End User (Pharmaceutical, Biotechnology, Medical Devices Manufacturers) – Global Forecast to 2020. Link
- Crescent Industries. (n.d.). Benefits of Cleanroom Injection Molding. Link
- Kaysun Corporation. (n.d.). The Future of Injection Molding. Link
- Alcami Corporation. (2023). Alcami Capabilities. Link
- ScienceDirect. (2023). Polymeric Biomaterials. Link
- NCBI. (2023). Application of Plastics in Medical Devices and Equipment. Link
- ScienceDirect. (2023). Cleanrooms. Link
- Medical Plastics News. (2023). How 3D printing is impacting the medical field. Link
- BBC News. (2023). The Future of Medical 3D Printing. Link
- Nature. (2023). 3D Printing for Medical Applications. Link
Get in Touch - We Can Help
Alcami combines different production technologies allowing us to provide a turnkey solution for a variety of parts. We combine this with sourcing and logistics services, so our customers don’t need to worry about shipping and storage.